My plan is to kick off my car’s electric conversion this winter. My chosen car is my Autobianchi Giardiniera, Dante. I’m targeting 3-4 months to complete the conversion. Beyond finding time for the project, it will take weeks to design and fabricate components like the transmission adapter plate and battery boxes. To start things though, I needed to figure out my electric drive system. And for that, I needed start with estimating my EV battery range.
I’m being honest with myself – battery range calculation isn’t a perfect science, and any numbers and calculations will be wrong (but hopefully close). Even if I knew exactly the aerodynamics of my car and its tire’s coefficient of friction, etc., I’d have a hard time accurately accounting for driving style, traffic, hills, weather, etc., etc., etc. Google people’s real world range for their Teslas, and you get an idea of how it varies. I don’t want to drive myself insane with analysis, so realistically I can only get an educated guess and go from there.
Design considerations
I found that EV system design is an iterative process. You’ll likely have to run through options (and calculations) many times like I did until you’ve balanced your needs (and wants). There isn’t a perfect answer – you just have to figure what fits for your application. Talk to as many people and vendors as you can, as there’s a lot to learn and it will only make your conversion better. After doing this paper design, I’m sure I’ll be schooled by the real world when all is done anyway.
I have my high-level guiding principles and goals, and I settled on a 100 km range goal (that’s about 62 miles for my imperial minded friends). This was chosen as I only want a local daily driver, but I didn’t want to deal with range anxiety when encountering hills and using the heater, etc. Now I needed to take a stab at designing a drive system and battery needs.
EV conversion system considerations
II already knew that I wanted to convert my Autobianchi Giardiniera, so I didn’t need to do the actual first step of picking a project ‘donor’ vehicle. Many will tell you to keep a donor car relatively small (light weight) and room for batteries (like a small truck). That said, a quick look will show you that people have converted many different types of vehicles. If you convert cars similar to others (eg like classic VW Beetles or Porsches), then you’ll get a feel for what your up against, as there is lot of info on these type of projects.
The equipment options for an EV conversion are virtually limitless. If you’re not careful, you could be paralyzed by your choices. You need to narrow the options a bit, so you can get to the real work. Here’s how I worked through my choices.
AC vs DC motors
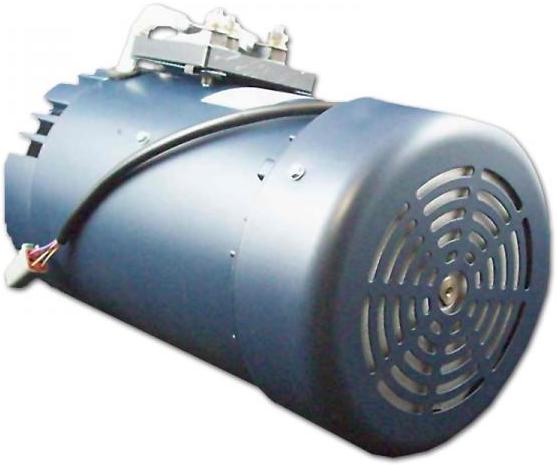
People started doing EV conversions with DC motors, as these were available from vehicles like old electric forklifts. Most people now use AC induction motors for safety reasons and energy regeneration when slowing. Since I wanted a regenerative system, AC was the way to go for me. That, and I wanted to stick with the crowd, as there would be more reference conversions that I can use for guidance. There are good reasons to go DC, like higher performance, so those who are interested should dig into DC system information.
Since I’m going with an AC motor I’ll focus on them. AC motors require a motor controller for a particular motor and nominal DC battery pack voltage combination. AC motors are often paired with a motor controller (like a Curtis controller), so that decision is likely made for you when you narrow down your motor choice and nominal battery pack voltage.
Horsepower
I started with with a rough horsepower (HP) requirement. Note that horsepower is not really the important spec, but it’s easy to use for a high level apples to apples starting point. My car has a rated horsepower of 17HP (yes, really, and it’s likely no where near that anymore!). I looked at the Fiat 500 horsepower curve in my handy Floyd Clymer workshop manual, and it maxes out around 4000 rpm. This gives an idea of what the car’s transmission is built for.
A common AC motor used in smaller car conversions is the HPEVS AC-34, but others had used AC-20 motors on classic Fiat 500s. This helped me narrow down motors a bit, but I had to run through battery pack sizing to make sure. If you don’t have a clue where to start, you could look at these and different motor performance curves for various battery pack voltages and amperages – like this one for an HPEVS AC-34 motor.
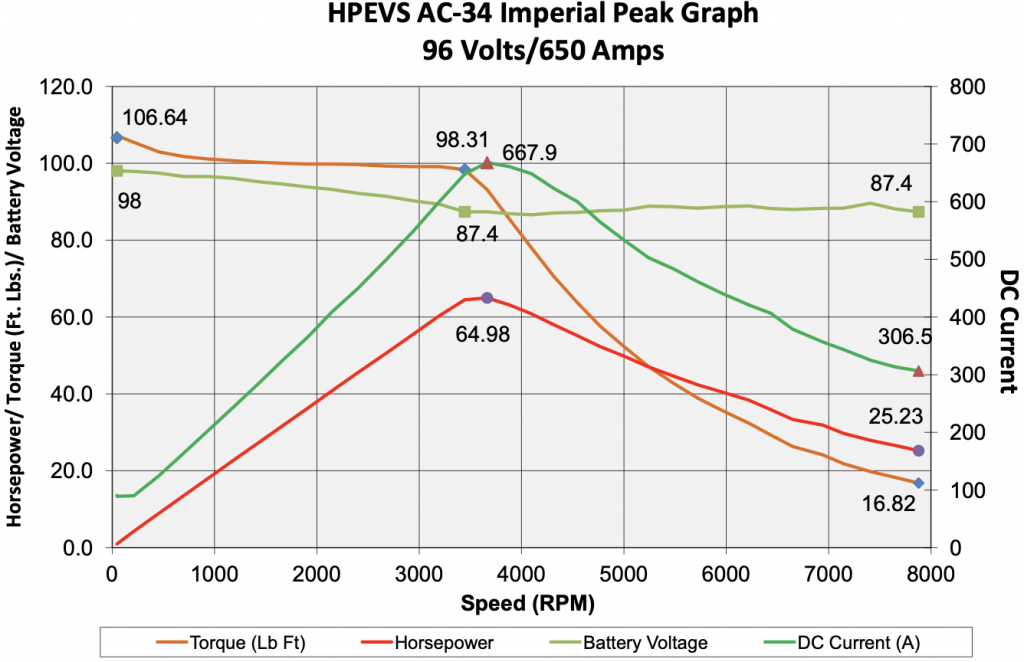
Battery pack
Most DIY EV conversions use lower battery pack voltages, ie from 96V to 144V (lower voltages than production EVs anyway). Batteries are usually connected in series to get to these voltages. For example, you can connect 30 3.2V batteries in series to get a battery pack of 96V.
Car manufacturers use higher voltages as they can provide better performance (both in terms of battery range and engineering design). But they have the luxury of building a car from the ground up (like integrating batteries into the sub frame of a car). For us looking to convert a car without a major car redesign, we’re limited to battery placement locations like engine compartment and trunk.
Battery options
There are many options for batteries, and more are becoming available as more EVs are being introduced. Many are new, and some are used ones recovered from vehicles like crashed Teslas, Nissan Leafs, VWs, etc. Tesla battery packs are well designed with best in class power storage for size. They also are more premium priced and are fairly large. People have had issues with fires with them, so that’s worth considering too.
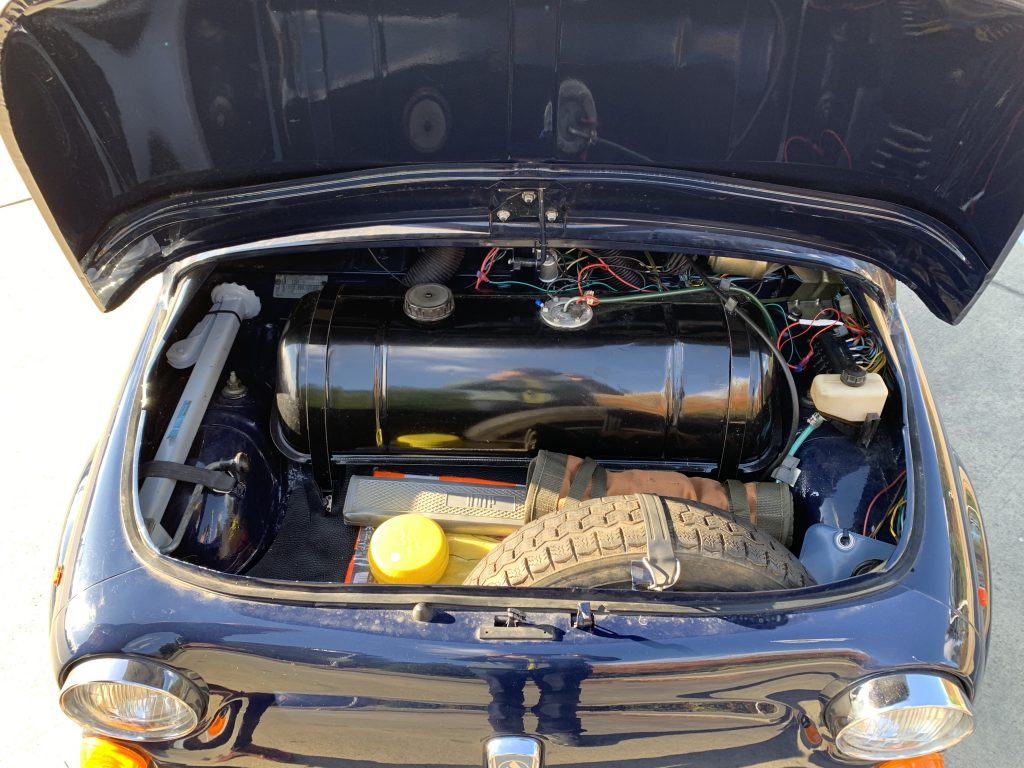
I didn’t like the dimensions of Tesla batteries for my project, as I thought I’d have to give up passenger space to make them fit. CALB LiFePO4 batteries are often a first option, as these are currently state of the art balancing battery characteristics and price. There are many CALB LiFePO4 options and sizes available. I looked at 3.2V 100Ah and 200Ah batteries, as my car is extremely space limited. (We’ll get into Ah, or amp hours, shortly.)
I started with considering a 96V system, since this was what it looked like most people used for smaller cars. As above, quick math tells you that you need 30 3.2V batteries for a ‘pack voltage’ of 96V. Scratching my head while looking into the engine bay (under the back storage in an Giardiniera) and front hood (gas tank and ‘frunk’ storage), I determined that I’d be lucky to squeeze in 30 100Ah cells, so that would be my starting point. (Spoiler alert: I’ve since changed to a 72V system, but it would take lots of sighing and many times through these steps to get to that decision.)
Ah (amp hours) and kWh (kilowatt hours)
After voltage, I looked at amp hours (Ah). Sometimes kWh (kilowatt hours) is given, but Power = Current x Voltage (P = IV), so you can convert to your preferred spec. These tell us how much energy is stored in the batteries. For example, a 96V pack with 100Ah batteries gives:
96V x 100Ah / 1000 W/kW = 9.6kWh
As stated above, any battery range calculation is suspect, but you have to start somewhere. I started with some rough math I found on-line for a Mazda Miata conversion that aligned with others’ range rules of thumb. It gave me a starting point, and I adjusted the math for my car’s weight against a 1990 Miata. I compared my math with other sources like classic Fiat 500 conversions, and it was pretty close, so I’ve stuck with it. Again, the proof will be in the pudding though.
Note: Don’t take my word (or anyone else’s) for anything – do your own math and estimates, as you’ll be the one stuck if your car runs out of juice before some theoretical battery range!
Power requirement
I do all my thinking and math in metric, but I’ll convert it for our Imperial friends at the end. To save an Internet search: 1 km = 0.625 mi, and 1 kg = 2.2 lbs. I’m also sometimes liberal with significant figures below, as I think this makes it easier to follow the math. (Kinda funny when you consider the estimate is suspect anyway!)
First, I needed to convert the Miata’s range estimate figure for my car. Specs say that a Giardiniera’s curb weight is 560 kg (1,230 lbs). I used 995 kg for my mystery Miata (I used a 1990 spec). The Miata example stated 162 km/kWh. So I converted this number for my car:
162 Wh/km x 560 kg / 995 kg = 91.2 Wh/km
Wh is just Watts needed per hour. You’ll use less when driving slow, and more when hammering the accelerator, but I used this as an average value, as I assumed city driving would be ‘average’. I also assumed that while Vancouver is quite hilly it won’t be much of an impact (and I’ll get some back from regeneration).
Battery range calculation
So, for my idealized car usage, I want a 100km x 91.2 Wh/km battery pack. This math comes out to 9.12 kWh for 100 km. 9.12 kWh divided by the 96 V (battery pack) gave me 95 Ah. Hey, that’s really close to what the batteries are rated for. Yay, small step forward: it looked like I could get my 100 km range target out of this 96V battery pack built out of 32 3.2V, 100Ah cells.
Another way to do the math is that those 100 Ah batteries together would give me a range of about 105 km. Due to the rough estimate I started with, this could be rounded to anything around 100 km, but for fun, let’s stay with the accuracy. I should also consider that my conversion will add about 40 kg net, but more than close enough for now.
Ok, for the imperial minded folk, I’ll do an example for my car using a 60 mi range (note 60 mi = 96 km):
91.2 Wh/km x 1.6 mi/km = 145.9 Wh/mi
60 mi x 145.9 Wh/mi = 8754 Wh
8754 Wh / 96 V = 91.2 Ah
Using the 96V 100Ah battery pack example:
96V x 100 Ah / 145.9 Wh/mi = 65.8mi
Since 65.8 miles is approximately 105 km, this jives with my metric calculations as expected.
A side note on parallel strings. I have a fairly meagre battery range goal, so one string of batteries with relatively low kWh works for me. I thought about using some of the latest LG Chem packs, but one serial string of these batteries for a 72V or 96V pack resulted in too low kWh values even for my application. Some designers get by this by using two parallel strings of batteries to double the Ah. While this is a valid idea, it isn’t to be done lightly. EV battery packs have a lot of available current, and things like eddy currents come into play and need to be addressed. Check out this Orion BMS article for more info.
Battery derating
Oh, but we need to derate batteries for the real world, isn’t this getting fun! 🤮 The first important consideration is that for healthy Lithium based batteries, we can’t use the whole battery. Yep, it is what is is though. If we drain Lithium batteries completely, we’ll damage them. This is referred to as State of Charge buffer. The rule of thumb is to use 80% for this. So either I have to take 20% off of my battery range, or I need a pack with 1.25x Ah. 80% of the 105 km is 84 km, still ok I guess, so I’ll stick with that 32 cell battery pack.
And what about ambient temperature? Well, batteries don’t like hot or cold temperatures. Luckily though, I live in a pretty temperate place. A cold day in Vancouver is around 0C (32F) and a hot day is 30C (86F) or so (but -10C and 35C+ happens occasionally, so I have to keep that in mind). Using info from Geotab, I used 80% temperature derating, as this mostly covered cold days and really hot days for Vancouver.
A side bonus is that for much of the year, Vancouver’s temperature would be in the over 100% rating for EV batteries. While I hope that is the case, I’ll design for the extremes to be safe. Again assuming I’m using a 96V 100Ah battery pack, I now have 80% of 84 km, or 67.2km of battery range when considering extreme weather. I should be happy though, as someone in Winnipeg might have about 40% of their batteries rating on a -30C day!
Battery life
Nothing lasts forever though, so we should consider that as batteries age, they lose ability to hold energy. This is due to general use (depletion & charging) and the ambient temperature when using them. High mileage use and hot climates are bad for batteries. I just used a rough number considering I live in a temperate place and don’t plan on high milage use or super quick, high-current charging.
Again based on Geotab’s data, I decided 10% degradation over 10 years would likely cover it. So now my 96V 100Ah battery pack would be 67.2 km x 90%, or 60.5 km. Not great, but this would likely (ok, hopefully) cover my range needs. (If buying used batteries, try to find gently used ones so that they’re not already degraded too much.)
If I put this all together, my batteries should be derated by around 58% (80% x 80% x 90%) to account for some real world battery pack issues. Some people just use the 80% State of Charge buffer and 10% for reserve for a total 72% derating, so I’ll keep that in mind too. That said, I’d rather be pessimistic with battery range estimates to help hitting the actual range goal.
Max current
All I needed to do was buy the gear and get to work, then eh? Well, no. I took a look at the amp rating of my target 3.2V 100Ah cells, and they we good for bursts of 300A. This is different to the amp hours, as the amp spec is the max current available a certain time periods. This is important when you’re accelerating; you need to pull a higher current out of the batteries to accelerate vs. when you’re coasting along. As a rule for Lithium batteries, it’s not recommended to pull more than 3 times the C Rating (100Ah for my target 3.2V cells) for more than 10 seconds. Google Peukerts if you want more details on rate of discharge info.
Looking at the performance curves for a 96V AC-34, 300A DC current would impact performance. For example, 300 A DC current would likely limit the motor to approximately 45HP vs 65HP from the 650A curve. I was fumbling with the current limiting and my target performance, when I realized I was dreaming if I thought I could fit in 30 3.2V cells into Dante without impacting the interior space anyway. Back to the drawing board…
OK, what about a 72V system
With further digging, I saw that a 72V system would meet my performance targets. I saw that others were doing similar systems for classic Fiat 500 conversions. So, let’s look at a 72V battery pack made from those same 3.2V 100Ah cells.
I’d use 24 cells, so I’d have a 76.8V pack at 100 Ah, or 7.68 kWh. I still use the 91.2 Wh/km estimate, so I would start my battery range at approximately 84 km. After my total derating value of 58%, I have a real world estimate of 49 km. On the worst day, that would be pretty range anxiety inducing. My best guess is driving a max 30km per day, but 49 km range is starting to get too close for my comfort. I’d have to charge often – at least every night.
While internally debating battery range anxiety, I decided that an HPEVS AC-20 motor would provide plenty of pep for my needs. At 72V, its a better performance target for my project. As a bonus its physically smaller than a AC-34, and I need all the space I can get to stuff all the EV parts in my car. Again though, that 300A max from the 3.2v cells was haunting me. Looking at the 72V AC-20 300A performance curve, I’d be looking at horsepower in the low 30s. This may be twice what my car has now, but I started looking at different battery options.
Torque
This is good time to discuss torque. Torque is usually only discussed by car performance enthusiasts. Until now, I’ve been using HP as the motor performance target. While it’s easy to use HP to compare car motors, it’s only a small part of the engine power story. At the start, I mentioned that my car’s horsepower is 17HP. This was taken from a graph showing 17HP at around 4000 rpm (revolutions per minute). ICE motors have their sweet spot for power at a rpm range and gears to help use this sweet spot. Torque is the twisting force of a motor – electric motors have much higher torque at low rpm than ICE motors. Also, electric motor power is much more impressive over a large rpm range – not just a sweat spot. For example, look at the orange line on the HPEVS AC-34 motor performance curve above. It has a lot of torque available as soon as the motor starts turning.
Often when people convert cars like mine, they simply run all forward driving in third gear. The electric motor’s torque is so high, we don’t need to shift though the gears to get up to speed. In city driving, it’s unlikely I’ll even have to shift into fourth, as the motor can also rev higher rpms. If you wanted to show off in a car like mine after converting to an EV, just start off in second gear and zip off the line. This assumes you don’t blow apart the poor old transmission designed for low power engines though!
OK, back to the HPEVS performance curves to look at torque. The HPEVS 72V AC-20 motor’s 300 A performance shows a torque of approximately 54 Nm (40 Foot Pounds) when starting off. The 550A curve shows 94Nm (69 Foot Pounds) starting off. Torque is a big part of an electric vehicle’s performance, so I may be limiting myself with 300A peak DC current.
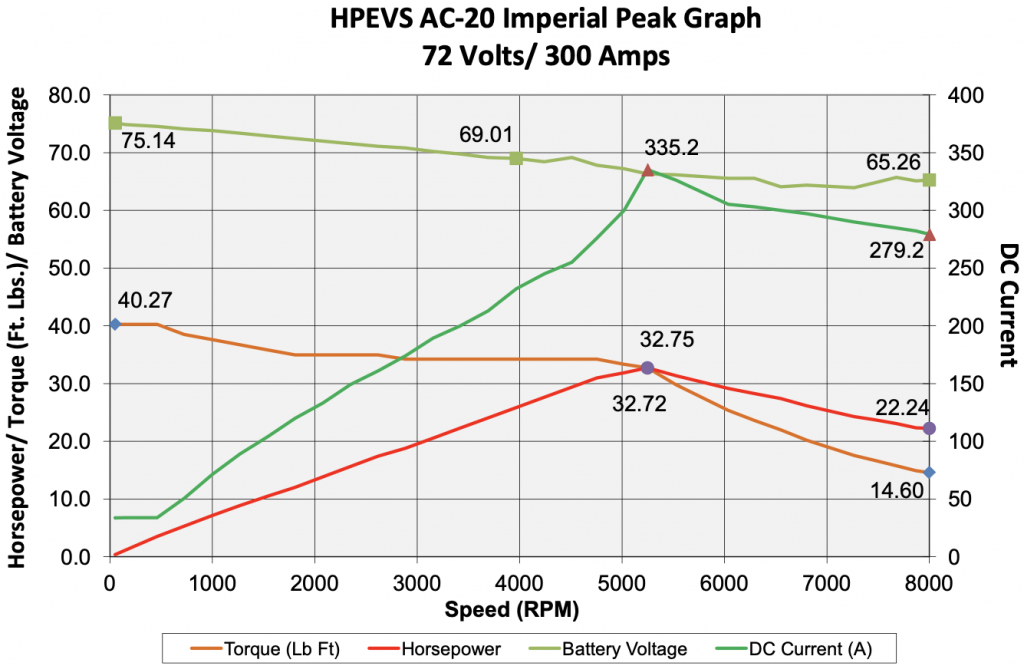
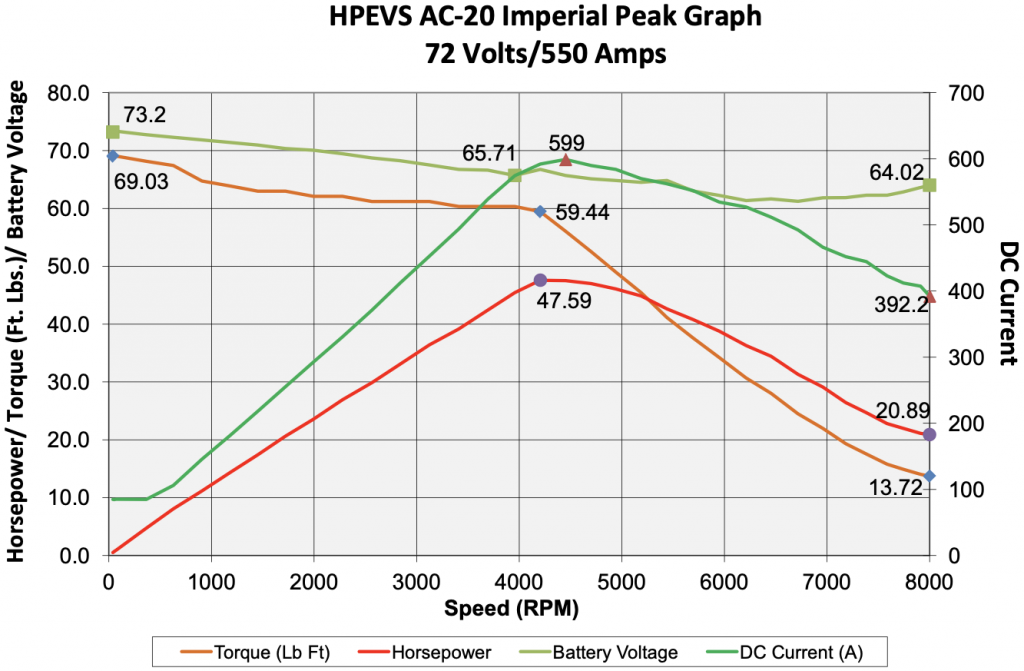
Battery options
I’ve settled on a 72V system, and I like the AC-20 motors performance (and small physical size). Something has to give to meet my system design goals though. I looked at 200 Ah 3.2V cells to make my range goals, but they would really impact my car’s interior space. This led me back to Tesla batteries. At first look, I didn’t think I could fit enough Tesla Model S battery modules in my car due to dimensions (height: 302.3mm, width: 302.3mm, length: 665.5 mm).
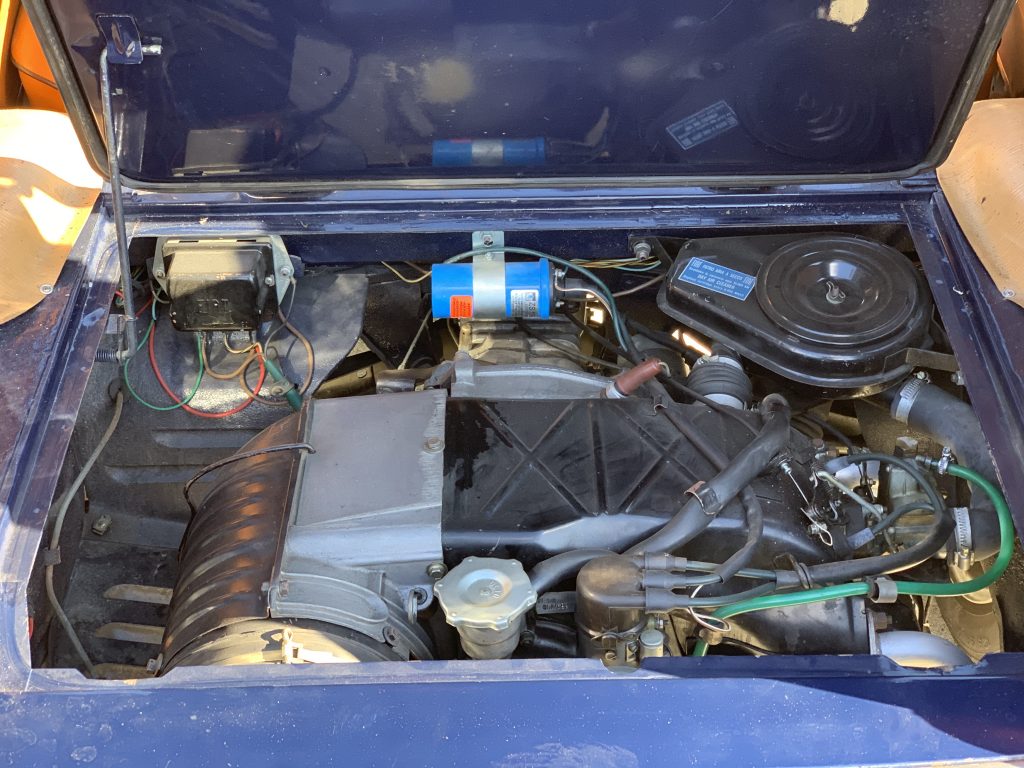
Other Fiat 500 conversions were able to fit one Tesla pack in the front (where the spare tire is) and two vertically in the back. Since an Gairdiniera has the motor compartment below the back storage, I didn’t think that would work, as I didn’t want batteries protruding into the back storage space. But something has to give, so it might be some interior space. Initial measurements show that I can fit one or two Tesla packs up front, and at least one above the motor. I’ll fit two in the back ideally, but I can’t be sure until the motor is installed. They are also reported to provide 500 amps and 750 amps peak allowing me to get the most out of the AC-20 motor.
Battery pack
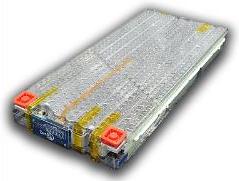
Great, I’m confident I can fit three Tesla S battery modules in my car in some fashion. This gives me a pack voltage of 68.4V which is close to 72V. Based on battery pack rated of 5.3 kW, I can calculate the battery range including derating:
3 packs x 5.3 kWh x 1000 Wh/kWh / 91.2 Wh/km x 58% derating = 101km range
Perfect (hopefully). I’ve done more research on-line, and this number aligns with others’ battery range estimates for classic Fiat 500 conversions. A classic fiat 500 is about 60kg lighter, but it’s a pretty good comparison. At the very least, I have alleviated my first level of range anxiety. Again, there is no guarantees with battery range, but I’m feeling pretty confident with my system choice.
I inquired with HPEVS and Curtis, and they confirm I can run at a pack less than 72V. Mine will have a nominal voltage of 68.4V. The HPEVS AC-20 motor with a 58-80 V Curtis controller fits these parameters.
Component cooling
An Internal Combustion Engine produces a lot of heat waste, but we should be aware of an electric vehicle’s cooling requirements too. Electric motors need cooling. In my case, the load is relatively low, so air cooling should be fine for the AC motor.
As all those electrons move out of battery packs, they too create heat too. Remember there’s a lot of current flowing, so the small resistances matter. My application should be pretty easy on the battery pack, so they can likely be air cooled as well. Note that many manufactures, including Tesla, have liquid cooling channels built in. These channels might be required if your motor demands high current, or maybe you want to heat your cells in colder climates.
The AC motor controller will heat up, and will require a aluminium cooling plate. I’ll also add a fan to cool the motor controller’s heat plate.
My EV drive system
Finally I had figured out my drive system. I ordered the HPEVS AC-20 & 58-80 V Curtis controller a couple months ago, and it should be in soon. While the drive system is critical, the other pieces are important as well. I haven’t touched discussing the other components like charger, DC to DC converter, heater, etc. I’ll follow up on my plan for these as well. CanEV, my ‘local’ EV parts source, has been helpful with these too.
I’m hoping my components won’t be further slowed down by COVID-19 supply chain issues and actually show up. To get a jump start, I’ve started working on the motor adapter and transaxle cover designs and talked with people that can help fabricate them.
This is getting exciting! It took a lot of muddling around, but I’m confident with my drive system choice and battery range estimate. I’ll update when I make some progress.
Stephen cooper
Really enjoying reading through your posts.
As a software engineer appreciate the level of detail you go to.
Planning to replace my aftermarket CarPlay stereo with a custom built unit so found some really use info in your posts.
Looking forward to see what your doing next.